Tips & Tricks to go faster
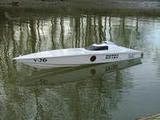
HELPFUL HINTS
Speed tricks are important, but reliability is even more so. Anything that improves a boat's reliability and run time will make it more successful on the racecourse or when running for fun at the local pond. One of the most basic requirements is to keep the electronics dry, yet often see boats that have taken on some water after only a few minutes' running. Water and RC gear don't mix; the boat not only might stop running well, but the equipment can be damaged and require costly repairs, too.
The best solution is to keep water out of the boat in the first place. This is easy with some designs, particularly if the boat has a tape-down hatch. In a race, fast boats will get well-splashed by others, but water can splatter the deck and seep into the interior even when a boat is running alone. Obviously, any boat that flips can take on lots of water if it isn't well sealed-it can even sink! Good tape is important. Popular types are electrical tape, clear "hockey" tape and 3M no. 190 clear plastic tape. It's expensive, but it sticks well and lasts without leaving a sticky residue. No matter which tape is used, the deck and hatch should be clean and dry so the tape sticks properly.
Water can enter the hull through any opening, but the main culprits are at the prop shaft and the rudder pushrod. To seal the space between the shaft (or flex cable) and the shaft tube, I use a short length of silicone fuel line slipped over the inner end of the tube. let some of the silicone extend past the end of the tube so it just forms a seal on the shaft. It doesn't take much contact between the silicone and the shaft to keep the water out, and too much contact will cause unwanted drag.
The rudder pushrod is another route through which water enters the hull. A rubber bellows seal such as the one from Bru Line* works well and allows for some misalignment between the pushrod and the rudder arm. use the flexible plastic tubing designed for nitro outboard throttle control. glue the outer tube to the transom and use the inner tube as the pushrod. Again, a short length of silicone fuel line forms a seal between the inner and outer plastic tubes.
A trick learned from racer Dick Crowe is to place the receiver inside a piece of food wrap or similar plastic film with a piece of folded paper towel, tying the opening around the wires with a cable tie. Then, even if water enters the hull interior, the receiver will be protected. This is not quite waterproof, but if just a little water enters the plastic, the towel will soak it up and keep it away from the electrics. It is important to open up the plastic when you've finished racing and wipe off any water on the receiver case. Other racers use rubber balloons to protect the receiver, but these are not completely waterproof either and are more difficult to open and dry.
POWER TRAIN
Our fast electric boats are power-limited, and anything we can do to reduce wasted power will make the boat go faster and run longer. One of the most common errors new boaters make is to neglect driveline alignment between the motor and the prop. often see sharp bends in the flex cable to correct poor alignment between it and the motor coupler or the strut. Tight bends put excessive force on the cable, shorten its life and greatly increase friction between the cable and the cable tube. When you build a boat, you often spend up to an hour installing the driveline, motor and strut to get perfect alignment between all of them. This extra time is paid back later with a faster, more reliable model.
Another power-robbing problem is associated with prop thrust transferred to the motor. All of the prop's thrust is transferred to the boat through the motor, and in most cases, the motor bearing/bushing in the endbell absorbs all the thrust. This is especially bad with stock bushing-equipped motors that were never designed to accommodate end thrust. The result is extra drag and friction, which heat up the motor and waste power. The solution is to fit a thrust bearing between the motor coupler and the motor case. High-quality thrust bearings can be found at most hobby stores; they are often used in RC cars. Less expensive bearings are sold by several model boat makers such as DPI* and Warehouse Hobbies*. When setting up this bearing, care must be taken to eliminate binding. Almost all motor shafts have some end play, and the bearing is set up with just a bit of play as the motor shaft is pushed and pulled. There must also be a small gap between the drive dog and the strut so the thrust is transferred to the motor. With this bearing in place, the motor will run cooler, and the boat will run faster and longer.
Some boaters prefer to take the prop thrust on the strut. The problem with this idea is that the flex cable shortens when it spins under load. Setting the cable statically with no play between the drive dog and the strut puts the cable in a bind as it shortens, and this induces lots of friction. It is very difficult to guess the correct amount of play to use, as the cable alternately shortens and lengthens as the boat accelerates and slows. Taking the thrust at the motor simplifies this problem.
Drive-shaft friction also contributes to power loss. It is very important to lubricate the solid drive shaft or the flex cable with the proper oil or grease. A relatively thin oil is needed on a solid shaft with its small clearances between the shaft and the stuffing tube; a waterproof grease or a thicker oil that will stick is best on a flex cable. I use Marvel Mystery Oil on my solid shafts and either Prather* cable grease or a mixture of 80WT gear oil and Prolong oil additive on my flex cables. Be sure to use lubricant, even with a Teflon liner. I will lube the driveline before each day of running and will often relube between heats in a big race. After each day of running, I'll pull the driveline out and dry it completely to prevent corrosion.
By the way, corrosion is another enemy of performance. I make it a point to dry off all of the model's parts after a day's running, including pulling all the internals if I know a lot of water entered the hull. use a hair dryer on the motor and radio equipment, and take the receiver out of its case to help it dry. this learned the hard way that rusty motor bearings will destroy performance; a motor used in an outboard had gotten wet repeatedly, but did not try to dry it out after each day- just let it dry naturally. In short order, the motor began to overheat, and performance deteriorated. I disassembled the motor and found that the bearings were badly rusted. Spinning the bearings resulted in an awful grinding noise; no wonder the motor overheated from the increased friction.
IMPROVED WIRING
All the power available in our boats is contained in the battery. The motor just converts that stored energy into mechanical energy to spin the prop. Getting as much of that energy to the motor as possible should be a goal of all fast electric boaters-it is "free" energy. A common error is to use too much wire when you connect the cells to the motor. Always use thick, multi-strand silicone wire of at least 14 gauge to reduce resistance, and plan your installation to reduce the length of that wire as much as is practical. Reducing wire length by 12 inches, which can be done in many installations, can increase voltage to the motor by 4 volt at high amp draws. This is around 15 watts of power, and for a 4-cell boat, this is an increase of more than 10 percent. Shorter is better, although it is not a good idea to shorten the wires so much that the installation becomes impractical. You still have to replace packs and motors.
THE HULL BOTTOM
The greatest limitation on a boat's speed is the friction between the hull and the water. The reason hydroplanes are faster than monos is because hydros contact the water less. Monos with steps usually are not allowed to race with non-stepped monos because the steps aerate the bottom, reducing friction and resulting in higher speeds. What can be done to reduce hull friction without redesigning the hull?
Some competitors will "blueprint" the bottom of their hull, making sure that it is perfectly flat and true. Fellow columnist Jerry Dunlap has devoted entire columns to the subject, but the idea is to fill in any low spots and sand down any high spots, then sharpen all the edges. This can be relatively easy to do on a hydroplane sponson but is more involved on a mono bottom with multiple strakes. I have experimented with "speed coats," that is, a paint that includes solid lubricants such as graphite. I've made these from thinned epoxy and colloidal graphite, painting the bottom then sanding it perfectly flat. This can be a lot of work, and I'm not certain that the effort is worth it. The graphite may reduce friction with the water, but more of an advantage is probably gained from the flatter surface with very sharp edges. Other racers have used spray paint that contains graphite; this is an easier way to get the solid lubricant onto the boat's bottom.
The tips and tricks above can improve the reliability and performance of your fast electric boat, and they are all practical for use on both raceboats and sport boats. Try a few of them, and see how well they work for you.